Honda’s second-generation NSX sports car, designed and manufactured in the U.S., has attracted significant attention thanks to its mechanical sophistication and the agile handling produced by its complex AWD drivetrain. Among its most notable advances is its deployment of torque vectoring on the front axle, through twin independent electric motors, to further sharpen turn-in response and to add a potential extra dimension to the chassis engineer’s set of dynamic tools.
However, the Honda – branded Acura in North America – is an exclusive and expensive mid-engined coupé, priced well into six figures either side of the Atlantic. Nor is it the first production model to make use of torque vectoring to improve handling dynamics – that honor went to the BMW X6 sports crossover some years back. The BMW, too, is a premium product, the type of vehicle where such innovative chassis refinements are the rule, rather than the exception.
For Ford, at a much more price-sensitive point in the market hierarchy, it was a rather braver decision to go with an advanced driveline for the new RS version of its originally front-drive Focus hatchback. The company needed to pitch in at a high level in the competition for top honors among ultra-high performance hatchbacks based on regular family models. This was especially true as the power race had been getting out of hand, with models such as the Mercedes A45 AMG breaching the 350 hp barrier – from just two liters.
Ford, therefore, ensured that its dramatically uprated 350-horsepower turbo engine was matched by a driveline and a chassis of equal stature. Developed in a transatlantic partnership between engineering centers in the U.S. and Europe, the Ford Performance AWD with Dynamic Torque Vectoring driveline took a fresh look at the challenge of delivering 350 horsepower without undue drama but, again like Honda on the NSX, with a keen eye on preserving the agility and yaw responsiveness that AWD platforms so often killed off.Central to the specification was a rear drive module which would contribute positively to vehicle dynamics, rather than simply taming the wildness of too much power to the front axle. Thus, twin electronically-triggered clutch packs on either side of the rear differential are able not only to control the vectoring of positive torque from left to right, but also handle the split of torque between the front and rear axles. In its current iteration, the maximum rearward torque bias is 70 percent, while to deal with extreme cornering situations the outside rear wheel can take the full 100 percent of the torque fed to the rear axle. The engine’s maximum torque on overboost is a substantial 470 Nm, which gives a useful idea of the forces involved.
As always, however, the physical hardware provides no more than the set of tools to enable the job to be done. What defines the all-important character of the vehicle is when, how and in what combinations each of those tools are used – in other words, the software and the programming that drives each element.
Here, Ford again chose an ambitious approach to make the most of the fresh hardware and the possible synergies it could offer between conventional brake-based traction control – which reduces the power reaching the road – and the non-power-sapping torque-vectoring AWD.
“This AWD system is a breakthrough technology, capable of delivering supreme cornering and handling at the limit,” says Dave Pericak, director, Global Ford Performance. “We have ripped up the rulebook which says that AWD hatchbacks cannot be fun to drive, and have created a car which will surprise and reward in equal measure.”
As an example of the dramatic impact these interactions can have on handling and cornering, the system is able to pre-emptively divert torque to the outside rear wheel in entry into a bend based on inputs such as steering wheel angle, lateral acceleration, yaw and speed. The rear drive unit can switch torque from one side to the other in 0.06 seconds and, says Ford, this torque transfer has the effect of “driving” the car into the bend, achieving improved turn-in and stability and virtually eliminating understeer.
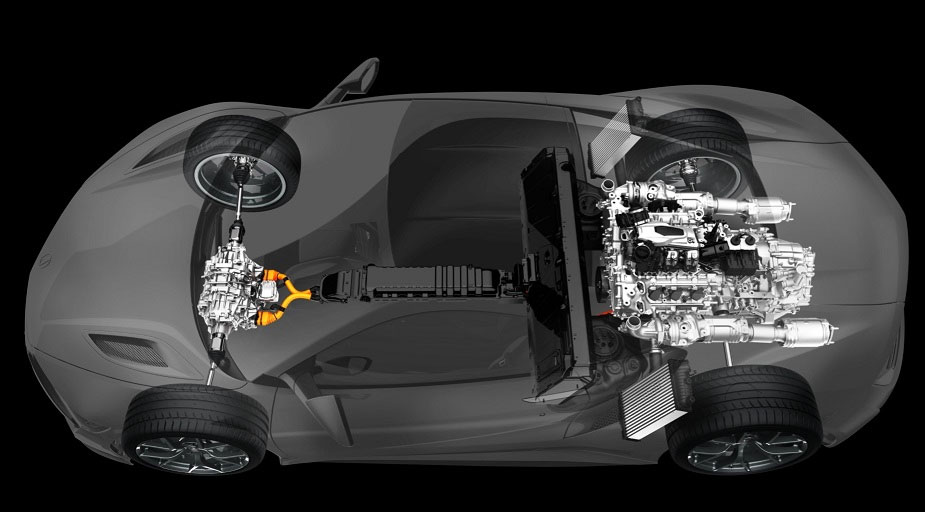
A further feature, which has attracted a lot of interest in the specialized enthusiast magazine community, is the RS’s Drift Mode. This setting, for track use only, biases torque to the rear and enables sustained power slides. Extrovert drivers and the tire manufacturers are sure to welcome this.
The optimum balance of drive torque between all four wheels gives the RS exceptional grip and enables it to record lateral acceleration values in excess of 1g – figures that are normally the domain of high-powered supercars with extravagant tire footprints. The real reward for the driver, however, comes in the shape of extra agility and responsiveness – precisely the characteristic felt to be lacking in other comparably-sized hot hatchbacks with AWD.
The same sentiment is echoed by Honda’s Ted Klaus, development team leader for the new NSX. “The direction we wanted to take for NSX makes the car undoubtedly a sports car because we wanted to create a synergy between the car and driver, rather than the car being in control,” he said in an interview published by the company. “We use terms like ‘direct response’ to convey what we mean. I would add to that ‘linear,’ especially when it comes to steering response. Competitors may have a linear steering response around center, while larger steering inputs give this unnatural non-linear effect. When you’re driving on mountain roads, perhaps on switchbacks, the car can become difficult to control. We wanted to give the driver a great sports car that provides a direct, linear, predictable feedback to their inputs.”
“As dynamicists,” continued Klaus, “we worked to ensure the car feels agile at slower speeds, but retains a feeling of security at high speed, particularly from the rear axle. This is a direction we took from the development of the original NSX. Other cars in this class, in our opinion, have low speed agility that translates into nervousness at high speeds, or high speed stability that makes the car feel lethargic at lower speeds. NSX is the only car to provide that agility at low speed, and security at high speed. We developed a setting to ensure the front and rear axles work together and give the driver a harmonious feeling. This builds a sense of confidence in the car for the driver.”
A prototype all-electric NSX, with individual motors driving each wheel, was specially developed for the dramatic 156-corner Pikes Peak hill climb in Colorado. Able to vector torque in real time between all four wheels, it finished in second place in the Electric Modified class at the 2016 event.
An entirely different, and much simpler, approach is that just being adopted by Mazda. Its G-Vectoring Control (GVC) system can be applied to any vehicle, front-, rear- or all-wheel drive, and works entirely through the vehicle’s software.
GVC operates in a very straightforward way to maximize the potential tire grip and thus steering response. The instant the driver begins to turn the wheel for a bend, the software reduces engine torque, thus shifting the load to the front wheels. This gives a sharper turn-in and steadier cornering, with less need to make minute steering corrections, even after engine torque is restored.
Mazda claims the system improves driver confidence as steering corrections are fewer in number and smaller in amplitude. Fatigue is reduced, too, claims the company, and evasive maneuvers are more stable and safer, especially in slippery conditions.