How It Works - The Role of Metalworking Additives
In a previous article, we talked about the types of metalworking fluids. Depending on the type of fluid, the base fluid consists of oil, water, or both. But modern metalworking fluids depend on a wide range of additives that collectively optimize the performance of the fluid to protect the workpiece and the tooling.
Let’s walk through some of the more common metalworking additives to understand how each impacts fluid performance.
Emulsifiers
For fluids that include both base oil and water, emulsifiers are necessary to effectively blend the two. By having a fluid that contains a blend of both oil and water, the result is often a fluid that effectively reduces wear while also cooling the tool and workpiece.
Lubricity Additives
Metalworking fluids must also reduce friction, and lubricity additives accomplish this by facilitating sliding contact between surfaces. Lubricity additives function through adsorbing onto metal surfaces to create organized boundary structures that help prevent metal-metal contact. These additives help minimize heat and the resulting damage it can cause.
.jpg?h=575&w=1118&hash=1B7A8C5B99ED933564FB4012EC0B780C)
Antiwear and Extreme Pressure Additives
A key requirement of a metalworking fluid is to reduce wear, and antiwear and extreme pressure additives play a central role in this regard. These additives react at moderate or extreme tool pressures to form a protective film on metal surfaces, minimizing direct metal-to-metal contact. The result is that these additives help reduce tool wear and improve workpiece surface finish. Effective formulating ensures that these additives cover a broad range of pressures and loads for more complete wear protection.
Corrosion Inhibitors and Rust Preventives
Not all fluids are compatible with various workpiece materials, such as ferrous metals, aluminum alloys, and yellow (i.e. copper-containing) metals. A simple example is the tendency for water to promote rust on steel surfaces. Corrosion inhibitors are often incorporated into a metalworking fluid to provide days to weeks of protection from such defects. After metal components are finished, rust preventives are often then applied to provide weeks to months of additional protection against similar defects from storage, transit, and environmental conditions around the world.
Questions about metalworking formulations? Ask a Lubrizol expert.
Defoamers
Foam is an enemy to metalworking fluid performance, as entrapped air bubbles prevent the fluid from contacting surfaces. Defoamers are additives that are suspended in the fluid and that act as “bubble busters,” ensuring more complete contact between the fluid and surfaces for optimal cooling and lubrication.
Biocides
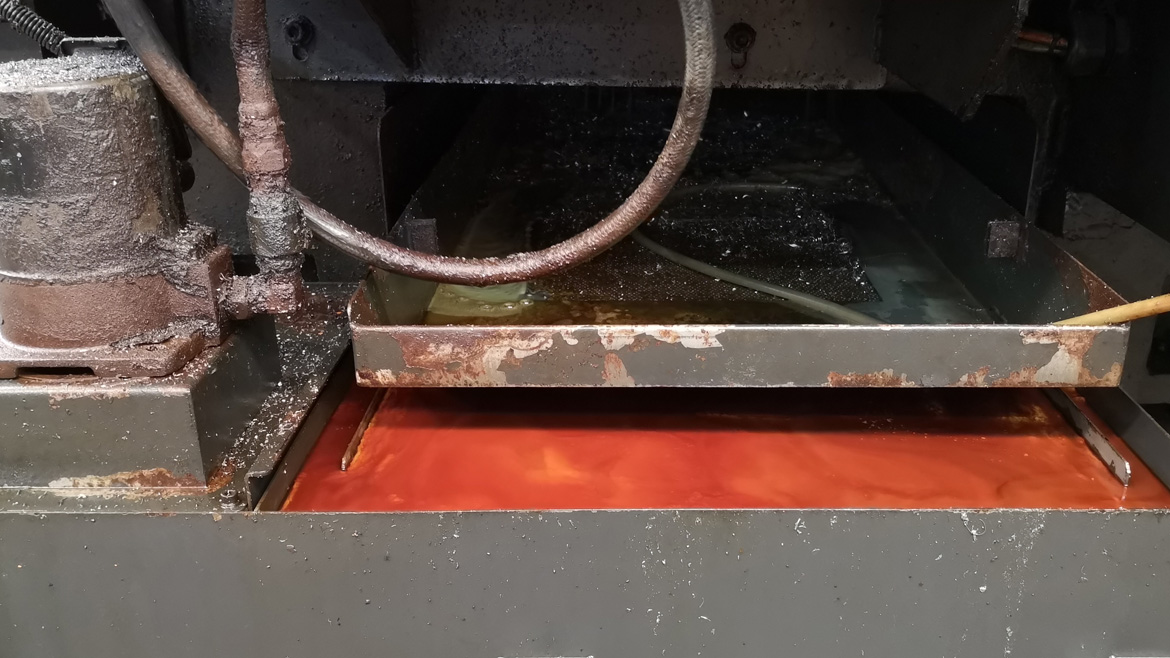
Metalworking fluids can be exposed to many contaminants in a manufacturing environment. Specifically for water-dilutable fluids, this creates a risk for bacterial and fungal contamination, which can hinder fluid performance and also pose a health risk to employees. Biocides are typically used with such metalworking fluids to protect against such growth, which helps ensure that the fluid has greater longevity. All these various additives are carefully formulated to ensure that, when mixed with the base oil and/or water, the result is a finished fluid that is optimized for the specific machine tool, workpiece and operation. However, all additives need to be properly chosen and balanced to work well together. Careful fluid formulating is therefore required to maximize the beneficial properties of additives while guarding against unintended performance traits.
See related articles to learn more: